Design Features
● Larger field of view than traditional 2D scanners simplifies the processing of larger parts
● Minimal spot distortion over the entire field of view minimizes processing variation for the highest quality laser-processed parts
● Air and water cooling options provide thermal stability and improve long-term accuracy
● Many choices of mirror surface treatments for a variety of laser wavelengths
Large Field of View with Minimal Spot Distortion
A unique optical design effectively controls the beam entrance pupil to be coincident for the X and Y scanner motion, increasing the effective numerical aperture of the scanner system. This design directly enables a larger field of view for a given focal length and reduces spot distortion over the entire working area. These advantages mean that the AGV-SPO is able to process larger parts faster and with greater consistency.
Design Configurations
The AGV-SPO is available with a selection of optical coatings and focusing optics to support a variety of commonly-used laser wavelengths and focal lengths. To support other needs, Aerotech can supply the AGV-SPO with customized optics and optical mounting features upon request. The AGV-SPO can be configured with air-cooled mirrors, water-cooled motors, or both. These active cooling features help to preserve working-plane accuracy in the presence of thermal disturbances caused by the laser as well as aggressive motion profiles.
Advanced Programming Features
The AGV-SPO utilizes all of Aerotech’s advanced motion and Position Synchronized Output (PSO) capabilities that have been developed for laser processing applications with traditional galvos and servo stages. Contouring functions such as Acceleration Limiting can be used to automatically reduce speeds in tight corners or small radii to minimize overshoot. The laser can be triggered based on the position feedback of the mirrors with PSO to ensure consistent spot overlap as the scanner changes speed.
Aerotech’s Infinite Field of View (IFOV) function seamlessly combines servo and scanner motion to extend the marking capability of the scanner across the entire travel range of the servo stages, eliminating stitching errors that can occur in a more traditional move-expose-repeat process.
|
AGV14SPO |
OPTICAL PERFORMANCE |
Beam Aperture |
14 mm |
Maximum Scan Angle |
±20° |
Beam Displacement |
35 mm |
Dither (Min. Incremental Motion)(2) |
0.3 µrad RMS |
Accuracy |
50 µrad pk-pk |
Repeatability(3) |
0.6 µrad RMS |
Gain Error |
0.05 mrad |
Non-Linearity |
0.01% |
DYNAMIC PERFORMANCE |
Tracking Error |
0 µsec |
Peak Acceleration(4)(5) |
60,000 m/s2 |
Continuous Acceleration(4)(6) |
20,000 m/s2 |
Positioning Speed(4) |
50 m/s |
Processing Speed(4)(7)(8) |
5 m/s |
Jump & Settle Time, 1 mm Move(4)(9) |
700 µsec |
STABILITY |
Long-Term Drift-Offset |
10 µrad/12 hrs |
15 µrad/24 hrs |
Long-Term Drift-Gain |
10 ppm/24 hrs |
Thermal Drift-Offset |
20 µrad/°C |
Thermal Drift-Gain |
1 ppm/°C |
MECHANICAL SPECIFICATIONS |
Weight |
5.1 kg |
Material |
Aluminum (Black Anodize and Blue Paint) |
MTBF (Mean Time Between Failure) |
20,000 hours |
Notes:
- All angles are optical unless otherwise specified
- Without air cooling option
- After initial 3-hour warm-up, ambient temperature variation < ±0.5 deg
- Typical performance with f = 160mm F-Theta objective
- Based on maximum rated current of the motor
- Based on rated rms current of the motor with water cooling option; maximum continuous acceleration is 70% of this value without water cooling
- Achievable with <1% velocity error over continuous velocity portion of move
- Marking speed is dependent on allowable tracking error
- Settled to within 1% of move distance
- All specifications are per axis unless otherwise noted
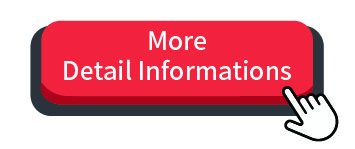